Not Only Meet but Exceed Expectations
Improve, Transform, Succeed
Our mission is to help businesses improve their processes, transform their approach to compliance, and thrive in competitive industries. By aligning your operations with your clients quality standards and implementing innovative strategies, we empower you to achieve excellence. Together, we redefine what’s possible, ensuring that quality becomes your advantage.
Exceed Expectations
7+ Years Of Undefeated Success
Years of delivering innovative quality solutions, MQC helps businesses achieve excellence in compliance, operations, and certification. Work with us to exceed expectations and thrive.
4+
Successfully Project Finished.
7+
Years of experience with proud
3
Branches
10+
Colleagues & counting
Exceeds Expectations
Quality Services
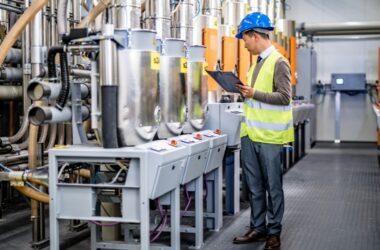
Quality Engineering Services
Quality Management Systems (QMS) Implementation: Design, implement, and maintain QMS in line with ISO9001/AS9100 standards to ensure consistent quality across all manufacturing processes.
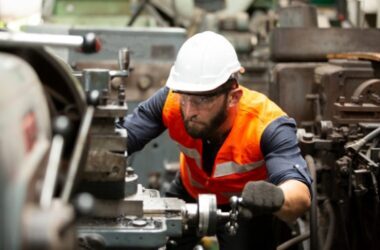
Process Optimization
Analyze and refine existing manufacturing processes to improve efficiency, reduce waste, and enhance product quality.
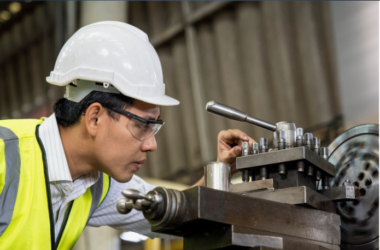
Change Management
Evaluate how the change will affect critical quality attributes, manufacturing processes, and end-product performance.
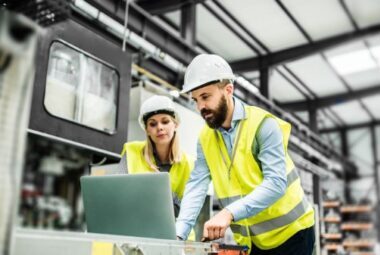
Materials Testing and Characterization
Material Analysis, Failure Analysis, Innovation, and Research Support
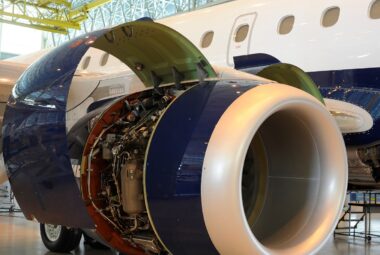
Manufacturing Process Improvement
Process Development and Optimization: Develop, review, and optimize SOPs to ensure they are both efficient and accurately reflect actual processes.
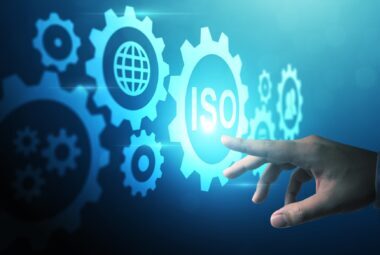
Compliance and Certification Support
Providing services to list clients in the Prime Manufacturers’ ASL and Non-Conformance Management.
Advanced Technology
Committed to Ensuring Quality, Safety, and Efficiency
We are dedicated to fostering sustainability and operational excellence in the aerospace and manufacturing industries.
We Follow Best Practices
Our commitment is to ensure processes, materials, and systems align with the highest standards of safety, efficiency, and environmental responsibility.
Exceptional Services
Transform Businesses
Contact us to schedule a visit or consultation with us at MQC. We’re committed to understanding and meeting your needs.
Canada
Montreal, QC
United States
Fremont, CA
Sweden
Gothenburg
About Founders
We Are a Leading International Company
Mohsen M. Amrei
CQE, Operational Manager
Hadi G. Nanesa
CTO
What Our Clients Say
Testimonials
General Manager
P. Mojdehi
Working with MQC was a game-changer for our organization. They played a pivotal role in developing and implementing our ERP system, tailored to meet the unique needs of our operations. The team was highly professional, responsive, and thorough, ensuring that every aspect of the system was aligned with our business goals.
Quality Supervisor
Z. Al-Salam
MQC exceeded all expectations in designing and implementing a robust delivery and quality management system for our company. From the initial consultation to the final rollout, their team demonstrated unparalleled expertise and attention to detail.
Request a Quote
Ready to Work Together? Build a project with us!
Learn More From
Frequently Asked Questions
Navigating the requirements of AS9100D can be challenging, especially when ensuring your quality management system aligns with the aerospace industry’s stringent standards. An AS9100D checklist is a helpful tool to guide you through the process, ensuring that all necessary requirements are met for certification.
However, a generic checklist often falls short of addressing the specific needs and unique challenges your organization might face. Every company is different, and achieving AS9100D certification requires more than just ticking boxes—it requires a deep understanding of the standard’s intent and how it applies to your particular processes.
At MQC (Materials Qualification Certification Inc.), we offer tailored solutions to help you achieve and maintain AS9100D certification. Our team of experienced quality engineering professionals can provide a comprehensive audit checklist designed specifically for your business. We go beyond the standard checklists by:
Performing a Gap Analysis: Identifying where your current quality management system stands against AS9100D requirements.
Providing Custom Guidance: Offering insights and recommendations specific to your operations to address any gaps and achieve compliance.
Streamlining Processes: Helping optimize your processes to not only meet AS9100D standards but also to improve efficiency and reduce waste.
Ensuring Continued Compliance: Assisting with internal audits, non-conformance management, and continual improvement strategies to maintain certification.
If you are looking for an AS9100D checklist that is more than just a list of requirements but a tool to enhance your operations and ensure successful certification, contact us today! We can provide a customized checklist, guidance, and support every step of the way, tailored specifically to your needs and goals in the aerospace industry.
Reach out to MQC for a consultation, and let’s discuss how we can support your journey towards AS9100D certification and continuous improvement in quality management!
Creating a comprehensive AS9100D checklist involves outlining key requirements from the AS9100D standard, which is a widely recognized Quality Management System (QMS) standard for the aerospace industry. The checklist can be used by organizations to ensure that they are compliant with the standard and to identify areas that need improvement before undergoing an audit.
Below is a checklist based on the main clauses and sub-clauses of the AS9100D standard. Each item should be reviewed to ensure compliance:
Context of the Organization (Clause 4)
4.1 Understanding the Organization and its Context: Has the organization determined external and internal issues relevant to its purpose and strategic direction?
4.2 Understanding the Needs and Expectations of Interested Parties: Has the organization determined the needs and expectations of interested parties that are relevant to the QMS?
4.3 Determining the Scope of the QMS: Is the scope of the QMS documented and does it consider all external and internal issues, as well as requirements of relevant interested parties?
4.4 QMS and its Processes: Has the organization established, implemented, maintained, and continually improved the QMS, including necessary processes and their interactions?
Leadership (Clause 5)
5.1 Leadership and Commitment: Are top management demonstrating leadership and commitment to the QMS?
5.2 Quality Policy: Has a quality policy been established, is it appropriate to the context of the organization, and is it communicated within the organization?
5.3 Organizational Roles, Responsibilities, and Authorities: Are roles, responsibilities, and authorities within the QMS clearly defined, documented, and communicated?
Planning (Clause 6)
6.1 Actions to Address Risks and Opportunities: Has the organization determined risks and opportunities that need to be addressed to ensure the QMS can achieve its intended outcomes?
6.2 Quality Objectives and Planning to Achieve Them: Are quality objectives established at relevant functions, levels, and processes? Are these objectives measurable and consistent with the quality policy?
6.3 Planning of Changes: Are changes to the QMS carried out in a planned manner?
Support (Clause 7)
7.1 Resources: Are necessary resources for establishing, implementing, maintaining, and improving the QMS determined and provided?
7.1.5 Monitoring and Measuring Resources: Are resources for monitoring and measuring provided, and are measuring equipment calibrated or verified?
7.2 Competence: Are personnel performing work under the organization’s control competent, based on education, training, or experience?
7.3 Awareness: Are employees aware of the quality policy, their contributions to the QMS, and the implications of not conforming to QMS requirements?
7.4 Communication: Are internal and external communications relevant to the QMS determined and implemented?
7.5 Documented Information: Is documented information required by the QMS controlled, updated, and retained appropriately?
Operation (Clause 8)
8.1 Operational Planning and Control: Are processes needed to meet requirements for the provision of products and services planned and controlled?
8.2 Requirements for Products and Services: Are requirements for products and services defined, including applicable statutory and regulatory requirements?
8.3 Design and Development of Products and Services: Are design and development processes established, implemented, and maintained?
8.4 Control of Externally Provided Processes, Products, and Services: Are controls in place to ensure that externally provided processes, products, and services conform to requirements?
8.5 Production and Service Provision: Are production and service provision processes controlled, and are there provisions for property belonging to customers or external providers?
8.6 Release of Products and Services: Are products and services released to the customer with appropriate documented information?
8.7 Control of Nonconforming Outputs: Are nonconforming outputs identified, controlled, and actions taken to prevent their unintended use or delivery?
Performance Evaluation (Clause 9)
9.1 Monitoring, Measurement, Analysis, and Evaluation: Are processes established for monitoring, measurement, analysis, and evaluation of the QMS?
9.2 Internal Audit: Is an internal audit program established, implemented, and maintained?
9.3 Management Review: Are management reviews conducted at planned intervals, and do they address the performance and effectiveness of the QMS?
Improvement (Clause 10)
10.1 General: Are opportunities for improvement determined and acted upon to enhance customer satisfaction?
10.2 Nonconformity and Corrective Action: Are nonconformities addressed, and corrective actions taken to control and correct them, and to prevent recurrence?
10.3 Continual Improvement: Is there an ongoing effort to improve the suitability, adequacy, and effectiveness of the QMS?
Additional Considerations for Aerospace (AS9100D-Specific)
Product Safety: Are processes in place to ensure product safety throughout the product lifecycle?
Counterfeit Part Prevention: Are measures established to prevent the use of counterfeit or suspect counterfeit parts?
Awareness: Are personnel aware of their contribution to product and service conformity, product safety, and the importance of ethical behavior?
Risk Management: Is there a documented process for managing risks to the achievement of applicable requirements, including processes for risk identification, assessment, mitigation, and acceptance?
Using the Checklist
This checklist can be used as a self-assessment tool during internal audits or as a preparatory step before undergoing third-party certification audits. Ensure that each item is reviewed thoroughly, evidence of compliance is collected, and any gaps are addressed with appropriate corrective actions.
If you need a more detailed checklist tailored to specific processes or operations, feel free to contact us!
AS9100D First Article Inspection (FAI) is a critical quality assurance process used in the aerospace industry to verify that a product’s manufacturing process can consistently produce parts that meet all engineering and design specifications. The FAI process involves a comprehensive, documented examination of the first production run of a new part or assembly to ensure that it meets the required quality and performance standards before full-scale production begins.
FAI is not just a one-time inspection but a thorough validation process that includes:
Dimensional Verification: Ensuring all part dimensions comply with engineering drawings and specifications.
Material and Process Verification: Confirming that the correct materials and processes are used as specified in the design requirements.
Functional Testing: Conducting tests to verify that the part or assembly performs as intended in its operational environment.
Documentation Review: Reviewing all associated documentation to confirm that every aspect of the production process is in compliance with the customer’s requirements and industry standards.
Why is FAI important?
First Article Inspection helps identify potential issues early in the production process, significantly reducing the risk of defects, non-conformances, and costly rework. It ensures product quality, compliance, and customer satisfaction—all of which are crucial in the highly regulated aerospace industry.
However, managing FAI activities can be complex and resource-intensive. It requires a deep understanding of the AS9100D standard, meticulous attention to detail, and comprehensive documentation.
This is where MQC (Materials Qualification Certification Inc.) comes in. With our expertise in aerospace quality management systems and AS9100D requirements, we can:
Guide You Through the FAI Process: From planning and preparation to execution and documentation, ensuring compliance and efficiency.
Conduct Independent FAI Audits: Providing an unbiased assessment of your FAI process to identify gaps and areas for improvement.
Support Ongoing Compliance: Helping you establish a robust FAI process that not only meets AS9100D requirements but also drives continuous improvement.
Don’t leave your FAI process to chance—contact MQC today to ensure your First Article Inspections are thorough, compliant, and effective. Let our team of experts help you streamline your FAI process, reduce risks, and achieve operational excellence. Reach out to us for a consultation and take the first step toward enhancing your quality assurance capabilities!